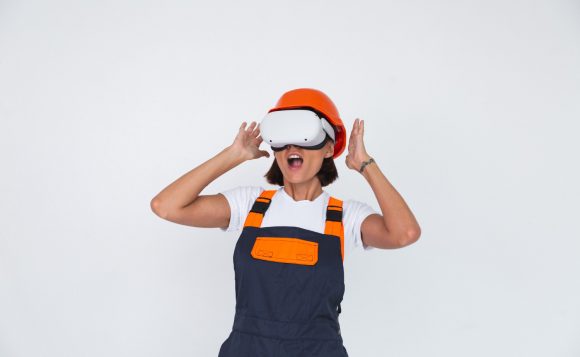
After COVID-19 negatively affected manufacturing, the industry is slowly coming back to normal. After all, we cannot ignore such factors as the shortage of skilled labor, the high cost of attracting new specialists, and quality employee training. These factors influence the current state of enterprises, and it’s vital for them to keep productivity and make a profit.
In today’s environment, more innovative ways of staff development are required. And these innovative solutions already exist. They are used by pioneering companies in the manufacturing field. It’s virtual reality that can help enterprises solve existing problems in employee training and give companies the advantages you will read about in our article.
VR Provides Realistic Experience
First of all, virtual reality provides a true-to-life training experience. Modern technologies allow for recreating a regular working environment, using photorealistic graphics and sounds.
For instance, manufacturing workers can improve their skills in VR Welding Training Simulator, a digital environment developed by Qualium Systems. According to Oleksii Volkov, head of XR department at Qualium Systems, the safety training app recreates the characteristics of exactly the same model of welding machine workers will have to deal with after they succeed in the training.
“Before being allowed to work with the welding machine, employees should pass safety training. These machines can have unique characteristics and different modifications. So, our app models all steps of handling the required welding machine from the beginning: how to connect the device, how to wear a mask, how to remove the safety lock, etc,” said Volkov.
How VR Reduces Turnover And Gives Confidence
A big number of manufacturing companies have always been using training methods, trying to reduce staff turnover and help new workers gain new skills. Respectively, there’s a new way to adapt employees and make them feel comfortable at their workplaces quickly.
VR can help the HR Department with it. Virtual reality training shortens the adaptation period. Let’s look at the example in the retail field: Walmart reduced training time by 96% with VR. It means, employees trained in VR headsets for only 15 minutes.
Employees gain new skills faster and feel more confident in a new workplace, as it was mentioned before. Thus, according to PricewaterhouseCoopers, employees increased their confidence by 275% after VR training.
VR Training Is an Effective Way To Save Money
Another key reason why companies use VR training more and more often is the possibility of saving money. Before virtual reality became popular, enterprises had been preparing separate rooms and special equipment to train manufacturing employees, taking much time and money.
According to PricewaterHouseCoopers statistics, 23 million workplaces will have a possibility for virtual reality training by 2030.
Virtual reality can help companies save money, since:
1) Instead of special equipment, enterprises buy compact VR headsets. The cost of devices and software, basically, depends on customer needs.
“There are a lot of factors to consider. What we are training on, what’s our starting point of training, whether we are getting onsite filming, whether there is the need to recreate something computer-generated. So, there are a lot of factors, that come into play when determining the cost. But, the entry point has gotten considerably lower. I think organizations that may have been considering e-learning or a video may actually dip their toe in the water with VR. Because it takes less than 100 hundred dollars to do VR program,” – said Nick Day, Roundtable Learning VP of Sales.
2) You can also save money by reducing training time. In our previous article about drivers of XR development in business, we described how manufacturers save 30 dollars per working hour.
3) VR programs can save workers and equipment resources since companies don’t have to hire a particular employee and learn them to control the whole training process.
“You can engage as many employees in the training process as you need at the same time. It would be better to buy 300 dollars Oculus headset and design the app, than, for example, hire a mentor and allocate special equipment and time. We can just place a group of people in the same room, and they will train. It’s safe and there’s no risk to life, and you can watch the training. We can also design the app, that will record current results, and you can see, how many people both successful and unsuccessful attempts,” said Oleksii Volkov head of XR department at Qualium Systems.
Reduce The Number of Manufacture Errors and Accidents
Manufacture accidents cause serious financial losses due to equipment damage and full production halt. Moreover, employees can be seriously injured or even pass away. In 2020-2021, the number of work-related fatal injuries in the UK reached 123.
Thoughtful and consistent VR safety training can reduce the number of accidents and save company money. When employees do the same exercise multiple times in a digital environment that maximally recreates their usual workplace, they actively develop muscle memory. Actually, they hone their work to the point of automation in order to reduce future risks.
“For technical skills to be retained and to guide long-term behavior, they must be stored and represented in long-term memory. We must train for retention. The best way to train for retention is to allow learners to practice the new skill often and to perfection. This process requires periodic testing of their technical skill proficiency, followed by targeted retraining of skills that they have learned poorly or forgotten,” said PhD Todd Maddox and Peter Campbell in their article.
So, when Ford implemented virtual reality training, the number of manufacture accidents was reduced by 70%.
Our new case — Chemical Safety Training Simulator — allows employees who deal with dangerous substances to train in virtual reality with no risk to their life and health.
“We designed an app, which doesn’t allow an employee to train in their place but recreates the workplace in 3D. It allows them to learn safety rules step by step. For example, how to twist the valves and under what conditions you should twist them to achieve the needed effect,” said Oleksii Volkov, the head of XR department at Qualium Systems.
Virtual reality for manufacture training offers a lot of advantages for many modern companies. VR increases employees’ productivity and confidence in their skills. Moreover, VR training can help companies save money by reducing purchasing equipment costs and the number of accidents on manufacturers.